Secrets of the casting method and process of Japanese samurai sword
19 Mar
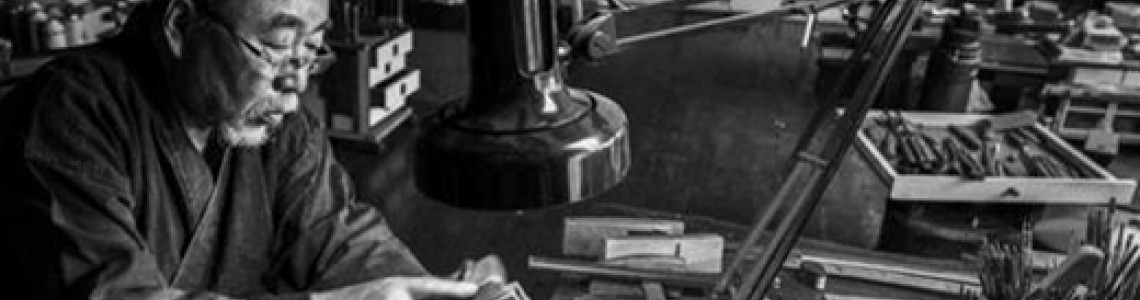
0 Comment(s)
3921 View(s)
Material selection and smelting steel
1 In Shimane, in the southwestern part of Japan, there is a rare ore called "the hometown of the gods" that produces special steel.
2 Smelting tools: The traditional smelting furnace, called the wind box, has a length of 3 meters, a width of 1 meter, and a height of 1 to 2 meters. There is a row of air inlets or blast openings on one side.
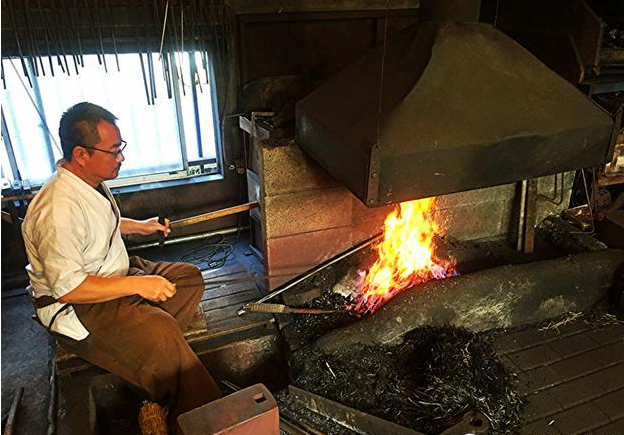
The process of smelting steel
1 The smelter must carefully observe the "black substance" (charcoal) used to forge steel in the furnace. The iron sand with the highest iron content produced locally is used for smelting, and the impurities of sulfur and phosphorus are very small, so as to ensure that the smelted steel and iron will not be destroyed by these impurities. The fusion of the carbon and iron sand in the charcoal in the smelting furnace will make it a special steel. The locals or knifesmiths call this pig iron "Jade Steel". The temperature of the furnace must reach 1,000 degrees Celsius.
2 During the smelting, the iron sand sinks to the bottom of the fire bed within an hour. The steelmaker can see from the color of the fire bed whether the iron sand has become "jade steel". It is necessary to ensure that the pig iron does not dissolve, which makes the samurai sword indispensable The chemical and physical properties of the product.
3 The iron slowly melts into the smelting furnace, and there is a combustion chamber 3 meters deep below the furnace. When the temperature reaches 1000 degrees Celsius, all the impurities will sink into the bottom of the combustion chamber, leaving only pure steel. The steel caster must learn to listen to the sound of the furnace by his ears. A good sword must have advantages other than elasticity: outer layer It must be wrapped with high-purity steel and there will be a small amount of impurities, such as sulfur, so the blade will be sharp. Containing a specific ratio of carbon and iron, it has both toughness and hardness, fusing hard steel and soft iron into a bimetal blade.
4 After three days and nights of smelting, the smelting furnace will be dismantled on the morning of the fourth day, and a bubble-like object (consuming 26 tons of iron ore and charcoal) is exposed in the furnace. This is the "Jade Steel" smelter. It is necessary to choose which parts can be sent to the swordmaker and which parts can only be used as knives and forks.
Forging process
1 Choose the material The smelter sends the selected material to the swordmaker. Then, the knifesmith personally examines and selects the heavy "Jade Steel" block with bright silver as the casting material. If it has gray-black chips or roughness, it will not work.
2 Forging process: Wrap the selected steel block with paper and then wrap it with a thin layer of clay and ash to prevent oxidation of the steel block. Reheat the steel block to 1300 degrees Celsius, and then break all the steel blocks into One piece (the action must be fast and the strength must be precise), so that the forging can remove the remaining impurities. The number of finished products is reduced by half compared to the original pig iron, and it becomes a whole piece of forged steel as a "sword blank". However, the forged steel block must be continuously folded to make the carbon distribution uniform, so that the metal raw material for the sword is completed. (The principle of this is to mix iron and steel so that the entire metal block is forged uniformly, and finally the carbon content of each part of the metal block is almost 0.7%). The knifemaker will estimate the carbon content based on the color of the steel. After continuous folding and forging, the knifemaker will have 5,000 layers of steel per centimeter (the texture formed by these layers is called "ground muscle"), and then slowly polish it. In the shape of a samurai sword.
3 There are two principles for the process of this creation: 1 The core of the samurai sword is softer because of the sharp blade. The blade will be weaker, so the swordsmith will choose a hard material for the blade. The back of the knife uses a soft material, which makes the knife have the function of hardness and toughness, which has the dual effect of sharpness and elasticity. 2 Then the two materials are merged. The hard blade with high carbon content is casted with steel. The inside contains softer iron with lower carbon content as the core part. The overall structure of the outer steel is called bolite and iron-hydrogen. Body in order to change the microstructure of the metal.
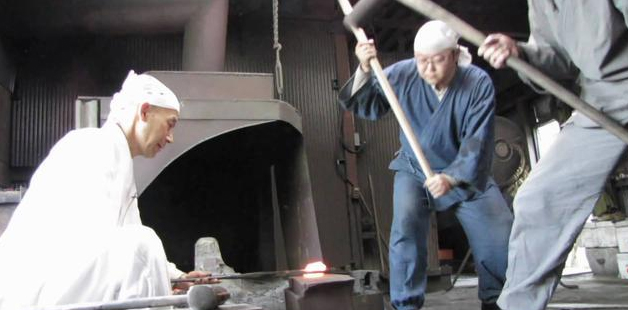
Steel clamping technology
4 Pack clay quenching: The sword maker mixes clay and charcoal powder evenly on the sword surface according to the secret recipe, which can isolate and protect the important parts of the sword during the hardening process. There will be at the intersection of the softer steel and the hard knife. An obvious line is actually "Hamon" (also an important symbol of high-grade katana). Then fire in a dark forging site (in the dark site, you can accurately determine when the temperature of the blade reaches the required temperature of 800 degrees, which is the best time, that is, when the blade reaches the bright red of the morning sun), quenching When using clean water, put the temperature of the blade into the water, so that the part covered with thin clay will quickly cool down and become very hard. The edge part covered with thin clay will quickly cool down like the carbon in the steel. With extreme pressure, this part will become the blade (note that the curvature of the samurai sword is not the curvature made by the swordsmith when making it).
The principle is: because the main body is covered with thicker clay, the cooling rate slows down, so it retains greater toughness. Structural changes during the cooling process cause the samurai sword to bend. A high-grade samurai sword has a crescent shape.
5 Rough grinding: Sometimes the swordsmith can decide the size and shape of the blade when initially designing the sword, and what the swordmaker needs to do now is to sharpen the blade out of the outline and sharpen the blade to meet the standard. In this process, the swordmaker will look at whether the sword has defects, and then decide whether to send the sword to the polishing master for the final stage of casting.
The above is the ladle mud technique of the top-grade katana, but the top-grade katana generally takes three people to build for three months.
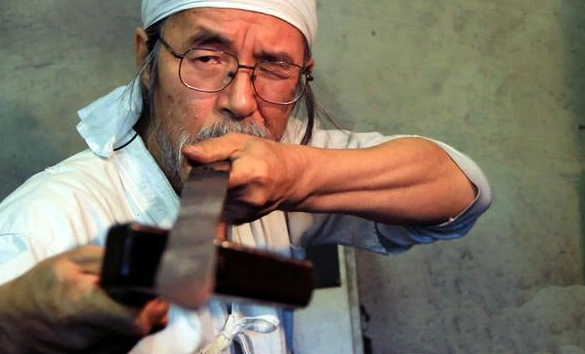
Grinding process
1 General grinding: The sharpener sharpens the sword here and sharpens the final shape of the samurai sword. Each katana must be sharpened with a different special stone. Note: The selection of Whetstone should be based on the characteristics of the various schools of making swords in Japan. To determine which whetstone stone to use. When sharpening the sword, the master must carefully search for the beauty of each katana and the exquisiteness of each sword-making genre when casting the sword. The rough grinding time is about 10 days.
2 Fine grinding: After roughly grinding, the sharpener will use a small stone to grind (about the size of a grain of rice). Generally, the grinding parts at this time are basically the polishing of both sides of the "Hamon" and the blade. At this time, be careful that it usually cuts your hands and also requires a lot of concentration. The time is based on the different schools of swordsmiths as a guideline, which is generally 6 to 8 days.
3 Overall grinding: The method of overall grinding is very mysterious. Every knife sharpener will try to keep it secret, so we can only know a general idea: the grinding master uses a unique method to grind the blade white, revealing the intersection of soft and hard steel. Line. In order to achieve the result of gradually showing the inner beauty of metal. The second is sharpening the tip of the sword. The specific method is the same as that of sharpening the blade, but with more care and concentration. But when sharpening the tip of the sword, each sword sharpener has its own unique secret recipe, so the final effect presented is also different. Then continue to polish for about 10 days to achieve the satisfaction of the polisher. Such a top grade japanese samurai sword is the real accomplishment.
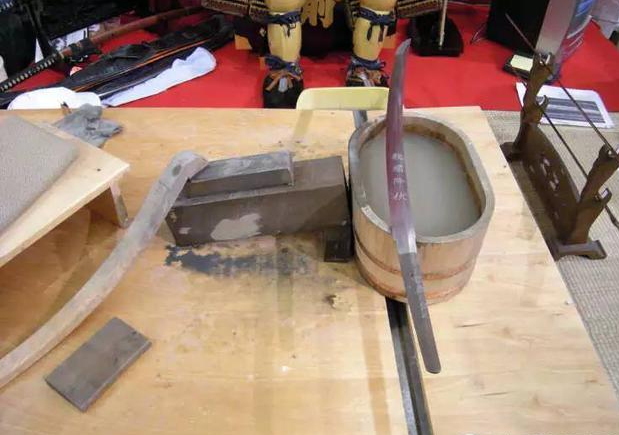
Want a unique sword? Feel free to contact us:
Phone: 086 13739276006
Email: [email protected]
Website: www.hanbonforge.com
Custom Sword Page: www.hanbonforge.com/CUSTOM-SWORDS/Custom-Your-Own-Swords
Phone: 086 13739276006
Email: [email protected]
Website: www.hanbonforge.com
Custom Sword Page: www.hanbonforge.com/CUSTOM-SWORDS/Custom-Your-Own-Swords
Leave a Comment