The secret of the traditional Chinese sword making process
23 Mar

0 Comment(s)
4624 View(s)
Forging
Put the matched materials into the furnace for heating, the steel block is opened and then folded and beaten, repeatedly forging. The number of folding and forging layers of traditional pattern steel, for example, the material before folding is 2 layers, 4 layers are folded once, 8 layers are folded twice... 2048 layers are folded 10 times, and so on, there are tens of thousands of layers. , Even tens of thousands of layers. Through this step, the sulfur and other impurities in the steel can be reduced and thinned. This is the Han Dynasty steelmaking technology, which is to repeatedly forge the raw materials (steel materials with different carbon content) as much as possible within a reasonable range to make The organization is more uniform and detailed, and the material is very strong. Different materials, different folding and forging methods, the shape and definition of the patterns obtained are also different, forming textures such as flowing water, feathers, pine needles, cow hair and so on.
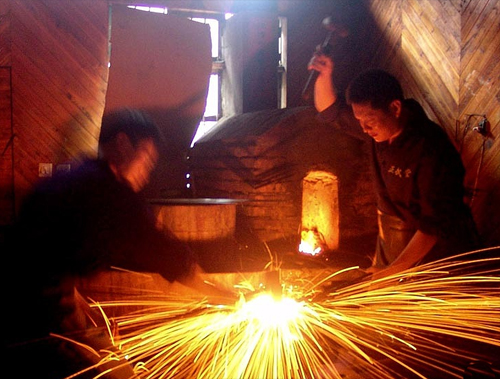
Complex
This refers to the technology of kobuse (inlaid steel) or clad steel used after the material is stacked and forged. The so-called good steel is used on the blade, it makes the sword have the effect of combining rigidity and flexibility, which can achieve good performance of being very sharp and not easy to bend and break under severe collision.
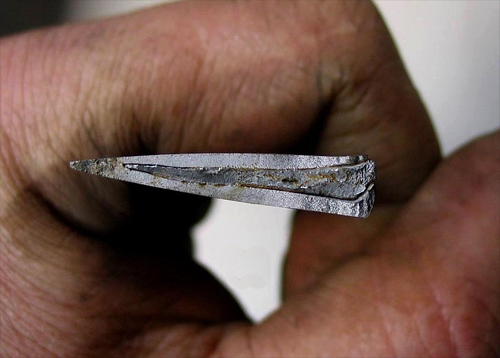
Forging billet
The composite material is beaten and prolonged into a knife or sword shape. At this stage, the prototype of the sword basically appears.
Use processing tools such as spatula, cutter, and file to trim the sword blank to make the shape and size of the sword meet the required requirements.
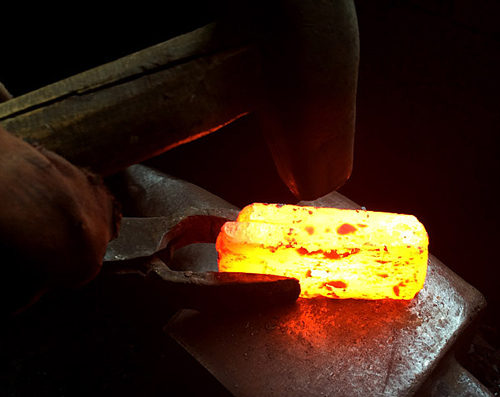
Quenching
This is the most critical process in the sword making process. The trimmed sword blank is burned red to reach a certain temperature, and then immersed in water to rapidly cool down. Through this step, the hardness and strength of the sword can be increased, so that the sword can be sharper. One step, the technical requirements are very high, and the temperature is determined by the artist's experience and the color of the flame. A slight error may cause the sword to crack, which will cause fatal damage to the entire sword. Depending on the material, different methods are used for quenching, such as overall quenching, partial quenching (clay tempered) and so on. After quenching, adjusting the curvature of the sword and rough grinding can proceed to the next process: grinding.
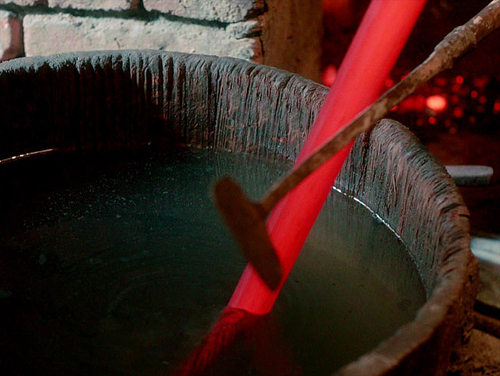
Grind
The grinding of a sword includes: coarse grinding, fine grinding, and fine grinding. The grindstone goes through more than ten processes from coarse to fine, until the blade is sharp, smooth and bright, ridgeline is straight, and groove line is standard. The sword body shows a "mirror" effect, and the cold light is compelling, and its pattern (forged or heat-treated hamon) is self-evident, which is very beautiful. The sharpening of a good sword is less than five or six days, and the more tens of days. It is slow and meticulous, and it is said that the work of sharpening a sword is twice as good as forging. The so-called "ten years to sharpen a sword" is an exaggeration, but it shows the importance of sharpening the sword in the craft of sword making and the effort spent. Finally, the artist will engrave his name, production year, etc. on the blade or blade. After these steps are completed, proceed to the final assembly stage.
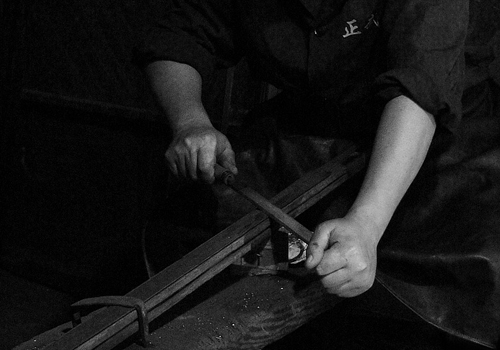
Assembly
With sheath: take the dehydrated wood, cut, slot, glue, and polish to shape. Some precious woods such as red sandalwood and rosewood are used as sheaths, and the wooden tires are painted or wrapped with fish skins, cowhides, etc. to prevent the sheath from cracking.
Equipment: The role of equipment is related to the wearing, use and decoration of a sword. It is made of copper, iron, even gold, silver, jade and other materials. The equipment of a sword can be roughly divided into sword head, sword grid (hand guard), sword jewel (hanging ring), sword jewel (sword dart) and so on. The material, decorative pattern and style of the equipment of the same sword should be harmonized to make it have a unique aesthetic value. Finally, the finished sword, scabbard and equipment are assembled into a whole, with the sword spike and wearing, placed in the sword cortex (cassette), and a Chinese sword is completed.
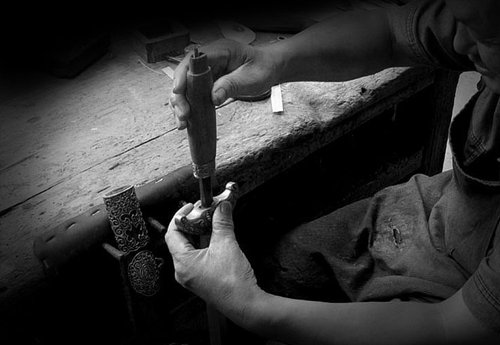
Want a unique sword? Feel free to contact us:
Phone: 086 13739276006
Email: [email protected]
Website: www.hanbonforge.com
Custom Sword Page: www.hanbonforge.com/CUSTOM-SWORDS/Custom-Your-Own-Swords
Phone: 086 13739276006
Email: [email protected]
Website: www.hanbonforge.com
Custom Sword Page: www.hanbonforge.com/CUSTOM-SWORDS/Custom-Your-Own-Swords
Leave a Comment