The process of making a samurai sword
04 Mar
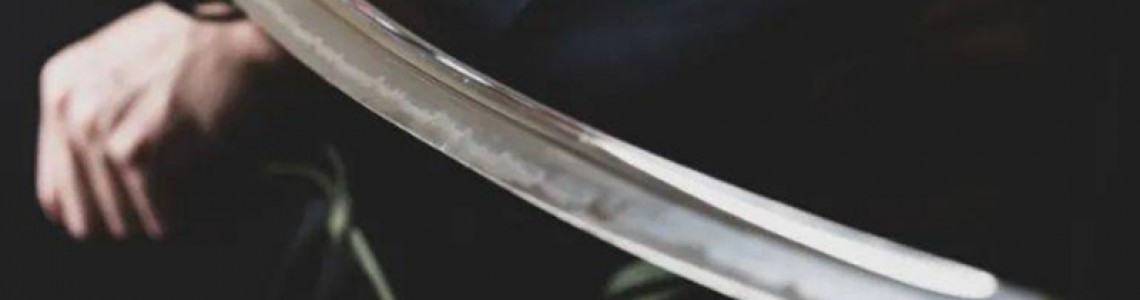
0 Comment(s)
3139 View(s)
Today, the artistic value of Japanese swords is getting more and more attention, but few people can tell the uniqueness of a sword. Authentic Japanese swords have a high level of technology in the manufacturing method. Generally speaking, they need to go through steel selection, smelting, forging, sword making, quenching, and grinding. The knife is equipped with a white wooden handle and sheath to save the blade for sale. swords such as handles, sheaths, and cylindric swords are installed in another trade, decorated by special metalworkers (tsuba crafts), and each has a famous teacher. The swordsmiths in Japanese history have their own factions, and some are the exclusive craftsmen of the shogunate and daimyo. The detailed steps are as follows:
Material selection and steelmaking
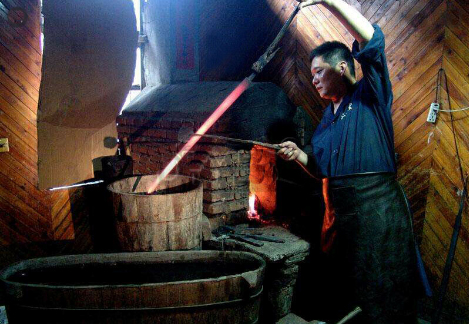
The raw material of Japanese swords is called Yugang (たまはがね, Tamahagane). Jade steel is made by traditional Japanese method. This is a low-temperature steelmaking method. The furnace temperature does not exceed 1100°C, which is far from reaching the melting point of pure iron at 1500°C. Although the melting point of ore containing impurities is much lower than that of pure iron, at such a low temperature, iron The ore is still difficult to melt completely.
Therefore, in order to obtain the ideal material and refine the impurities, the Japanese swordsmiths used sand iron with a surface area much larger than that of the large ore in the smelting raw materials, in order to better melt the ore, but at the same time the refining time also changed. It is quite long, and often requires three days, three nights or even seven days of uninterrupted melting.
After spending a lot of time to make a furnace, it is necessary to continuously use charcoal to burn it, and it must be refined at a low temperature, so that the purest effect can be achieved at a low temperature. Put sand iron on top of the charcoal, then another layer of charcoal, and then another layer of sand iron, layer by layer, and burn it for several days under different fire conditions and temperatures, at least three consecutive days and three nights, and then on the first Four mornings, the smelting furnace will be dismantled, revealing a bubble-like object in the furnace that looks like lava (consuming 26 tons of iron ore and charcoal). At this time, the "Jade Steel" smelter must choose which parts can be sent to the knifemaker. Go for a knife.
Forging
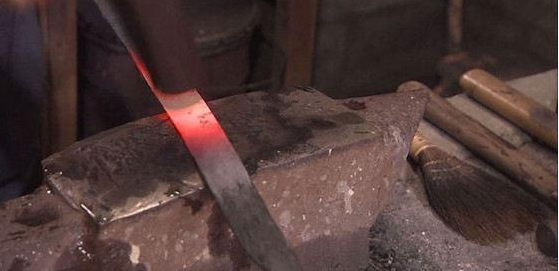
This is an important process in the Japanese sword making process, that is, the first step in making a sword. It means that the swordsmith heats the steel material to crimson for beating and forging. The steel block is opened and then folded and beaten. Repeatedly, the steel material can be stretched. Through this step, impurities such as sulfur and excess carbon in the steel can be removed to increase the elasticity and toughness of the steel.
This is like kneading noodles. The more layers of beating, the more uniform carbon and various components in the steel. The iron crystals will also be finer, and the final forged steel will be of uniform quality, reaching thousands of layers, very strong, and will eventually become a steel with uniform texture.
When it comes to the number of folds, there are generally two understandings. One kind of understanding is the number of times that the forger actually beats the jade steel with a sledgehammer. Then if the jade steel is beaten a thousand times, the jade steel will be decarburized during the forging process, causing the carbon content of the blade to become almost zero, and it cannot be used as a knife material. . Another kind of understanding is the actual number of layers that the jade steel is folded.
Forgers hit the jade steel billet in different ways, so the carbon distribution in the blade blank is different, and the places with more carbon will be darker, so different textures such as waves, kinks, tree rings, etc. will be formed. These textures are called "ground muscles" (地肌じはだ) after polishing, the ground muscles will appear on the body of the knife. When viewing, the light is best to shine from your back and top.
Clay tempered and quenching process
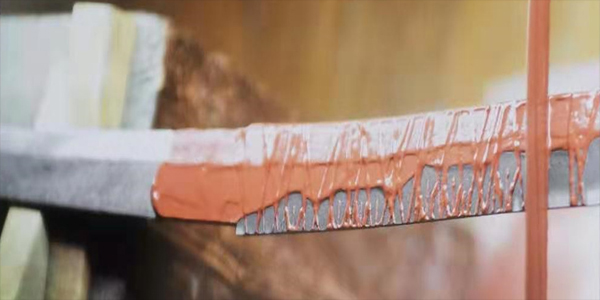
Quenching is the so-called heat treatment, and it is called water reduction (Mizuheshi, Mizuheshi) in Japan. From the perspective of modern material science, this step can be regarded as a knifemaker's method of controlling the carbon content of steel.
In order to make the blade have good elasticity and keep the blade hard and not easy to chip, Japanese swordsmiths will use clay, charcoal powder and whetstone powder according to the secret recipe to prepare burning blade soil, and then evenly spread it on the surface of the blade. It can be hardened during the hardening process. Insulate and protect the important parts of the blade. There will be an obvious line at the intersection of the softer steel and the hard blade inside. In fact, it is the "haber pattern" (also an important symbol of the top-grade samurai sword).
Then fire in a dark forging site (in the dark site, you can accurately determine when the temperature of the blade reaches the required temperature of 800 degrees, which is the best time, that is, when the blade reaches the bright red of the morning sun), quenching When using clean water, put the temperature of the blade into the water, so that the part covered with thin clay will quickly cool down and become very hard. The edge part covered with thin clay will quickly cool down like the carbon in the steel. With extreme pressure, this part will become the blade (note that the curvature of the samurai sword is not the curvature made by the swordsmith when making it).
The principle is: because the main body is covered with thicker clay and the cooling rate slows down, the structural changes during the cooling process cause the samurai sword to bend due to the preservation of greater toughness. A high-grade samurai sword is bent to the shape of a crescent.
Grind
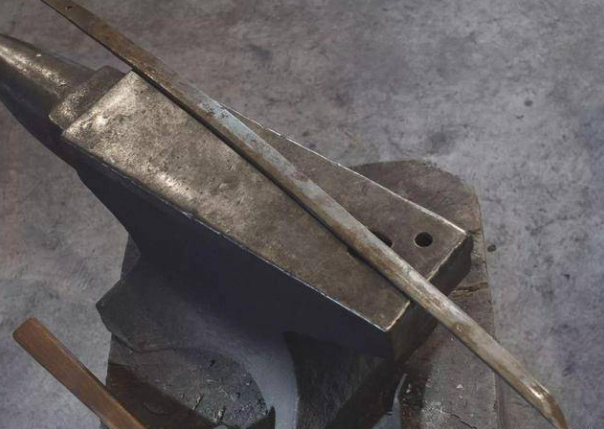
At this point, the knife is basically shaped and needs to be transferred to more detailed deep processing. A top-notch Japanese sword cannot only focus on the beauty of the sword or the cutting ability of the sword. The balance between cutting ability and aesthetics is always the core content of grinding.
The first stage of polishing is to modify and reshape, the main purpose of which is to sort out the shape and polish out the preliminary form of the work. The number of steps in this stage varies depending on the target. For example, if a newly forged knife is reground with a finished sword, there is a difference. For newly-made swords, there is no need to remove floating rust on the surface and rust spots that may penetrate into the blade, but to correct some forging defects, such as forging marks or uneven pick lines, which requires the use of multiple tools and processes. Antique knives may have other problems, such as side bends, which cannot be returned to the furnace or cold forged, otherwise the body of the knife will be severely damaged or even the crystal structure will be changed, so it is a very technically demanding process.
The second stage is fine grinding: After roughly grinding, the sharpener will use small stones to grind, (each stone that is only cut is only about the size of a grain of rice to grind). Generally, the grinding parts at this time are basically the polishing of the two sides of the "sharp" and the blade. At this time, be careful that it usually cuts your hands and also requires a lot of concentration. The time is based on the different schools of knifesmiths as a guideline, which is generally 6 to 8 days.
The third stage: The method of overall grinding is very mysterious. Every sword sharpener will try to keep it secret, so we can only know a general idea: the grinding master uses a unique method to grind the blade white, revealing the intersection of soft and hard steel. Line. In order to achieve the result of gradually showing the inner beauty of metal. Secondly, the specific method of sharpening the tip of the knife is the same as that of sharpening the blade, but with more care and concentration.
However, when sharpening the tip of the sword, each sharpener has its own unique secret recipe, so the final effect presented is also different. Then continue to polish for about 10 days to achieve the satisfaction of the polisher. Such a top grade samurai sword is the real accomplishment.
The general swordmaker engraves his name, residence, and production year on the stem at the end. Strictly speaking, the inscription is "cut" or "chiseled" on the stem by a sharp tool. Generally, the name of the sword's workmanship and domicile are on the surface (the outer side of the sword is a watch), and the year and month of manufacture and the name of the holder of the knife are on the inside. However, exceptions are common.
Want a unique sword? Feel free to contact us:
Phone: 086 13739276006
Email: [email protected]
Website: www.hanbonforge.com
Custom Sword Page: www.hanbonforge.com/CUSTOM-SWORDS/Custom-Your-Own-Swords
Phone: 086 13739276006
Email: [email protected]
Website: www.hanbonforge.com
Custom Sword Page: www.hanbonforge.com/CUSTOM-SWORDS/Custom-Your-Own-Swords
Leave a Comment